Real-time analytics from Edge to multiple factories with NATS and i-flow
Jan Strehl — July 22, 2024
In the competitive landscape of the manufacturing industry (e.g., automotive), achieving efficient and scalable operations across multiple factory locations is critical. This case study examines the implementation of a real-time analytics solution using NATS and i-flow to overcome common challenges such as data silos, real-time processing requirements, scalability, and communication inefficiencies in OT/IT environments. The primary design goal was to seamlessly scale real-time analytics across various factory locations.
Challenge
There are several critical challenges that typically hinder operational efficiency and scalability through real-time analytics:
Data Silos Integration Difficulties: Integrating data from disparate sources and systems is challenging, especially when dealing with a wide array of equipment and software. Fragmented OT Data: OT data is fragmented across various factory systems, leading to inconsistencies and difficulties in data management. Legacy Systems: The presence of legacy systems further complicates the integration process, requiring customized solutions.
No Real-Time Processing: There is an urgent need for real-time data processing and analysis to optimize manufacturing operations. Delays in data availability hinders timely decision-making and operational adjustments.
No Scalability: Integrating operations including thousands of machines and dozens of IT systems increases the volume of data. Existing infrastructures struggle to manage this growth efficiently while maintaining the flexibility to adapt.
Unreliable Communication: Ensuring reliable and effective communication between factory systems and enterprise-level applications is key. Today’s fragmented OT/IT infrastructures across sites hinder seamless connectivity and real-time data processing.
Solution
NATS serves as the edge and enterprise-level messaging system, ensuring seamless and reliable communication across all levels of the organization. i-flow functions as the connectivity, harmonization, and NATS publishing layer for OT data, effectively integrating and standardizing data from various sources before publishing it to NATS for real-time processing and analysis.
Why NATS?
- High throughput NATS is capable of handling high volumes of data, which is essential for scaling operations across multiple factory locations. This high throughput capability supports the increasing data demands as more machines and systems are integrated.
- Reliable Communication NATS ensures reliable communication between different components of the manufacturing system and across all enterprise levels. This reliability is vital for maintaining seamless operations and ensuring data integrity.
- Scalability The architecture of NATS allows for easy scalability, accommodating the growth of the company’s manufacturing operations. As new factories and use cases are added, NATS can integrate them into the existing system without significant reconfiguration.
- 100% deployed on premise NATS is easy to deploy and scale without the need for black boxed Cloud based services. This provides maximum confidentiality to the end user.
Implementation Steps
OT Connectivity with i-flow:
i-flow is deployed at Factory Edge level to provide bidirectional connectivity for real-time data exchange and integration between NATS and various OT systems. This includes PLCs, SCADA systems, MES and sensors.
Harmonization with i-flow:
i-flow harmonizes the OT data, ensuring it is consistent and standardized across different systems. This process involves cleaning, transforming, formatting and normalizing the data.
Publishing and Subscribing Data with i-flow:
i-flow publishes harmonized OT data to NATS, enabling real-time data streaming from OT systems to enterprise applications. Additionally, i-flow subscribes to data from NATS, facilitating bidirectional communication between OT systems and enterprise-level applications.
Edge and Enterprise-Level Data Processing with NATS:
- Messaging: NATS acts as the messaging backbone, providing low-latency, high-throughput messaging capabilities. It ensures reliable communication between different components of the manufacturing system and across all enterprise levels.
- Real-Time Monitoring: Enterprise applications subscribe to relevant topics on NATS to receive real-time updates from the factory floor.
- Analytics and Reporting: The data is processed and analyzed to generate insights, which are used for decision-making, predictive maintenance, and optimizing production processes.
Architecture
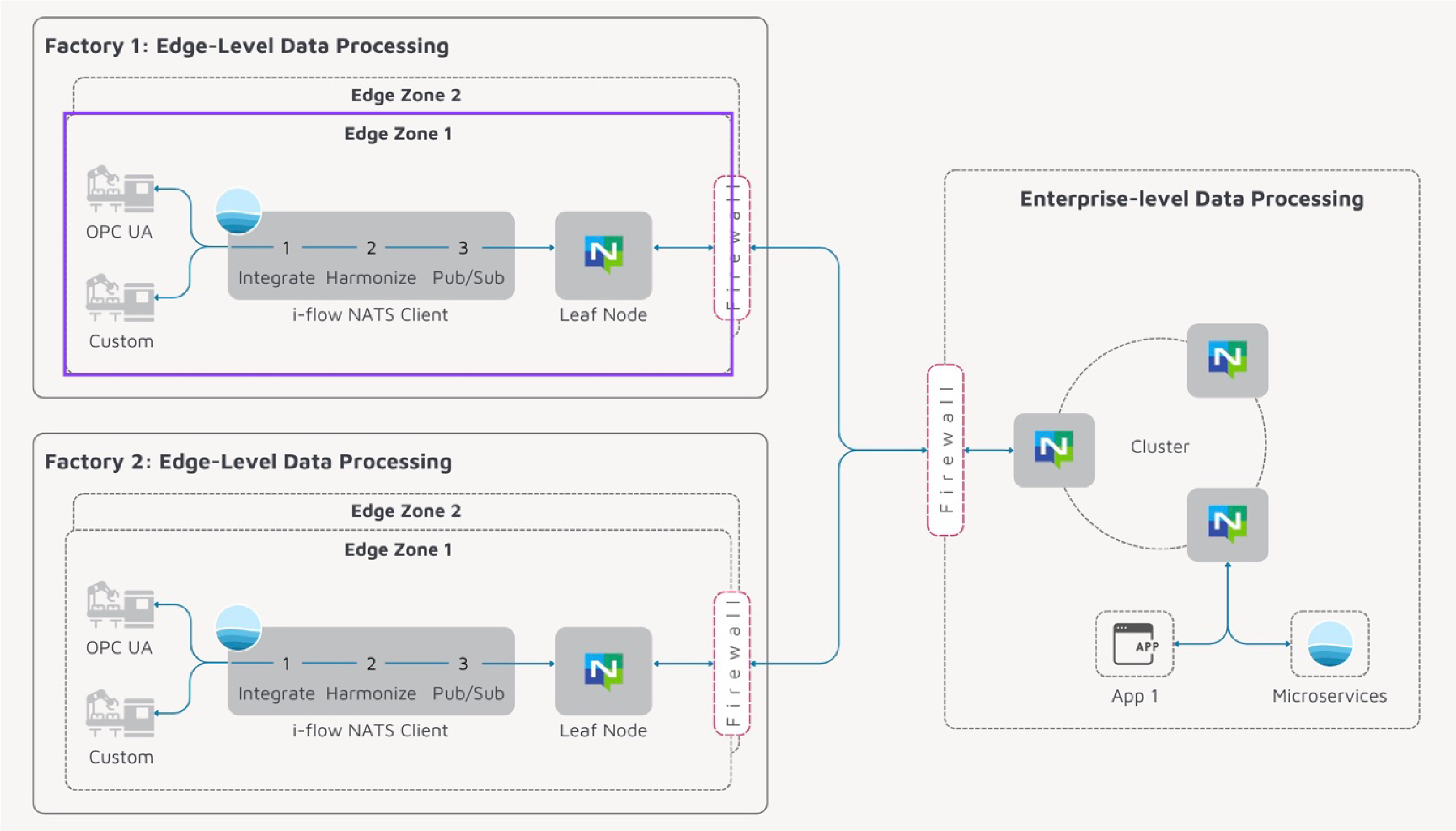
Benefits
The implementation of NATS and i-flow brings significant benefits to customers and improves key aspects of their digital infrastructure.
Improved Efficiency
Real-Time Data Integration and Processing: The integration and real-time processing of data leads to more efficient manufacturing operations by ensuring that critical information was always up-to-date and readily available. Faster Decision-Making: Real-time insights from the factory floor enable faster and more informed decisions and optimize the response to operational challenges.
Enhanced Data Visibility
Centralized Data: The centralized data repository provides a holistic view of manufacturing operations across multiple locations, enabling better monitoring and management. Improved Production Metrics: The enhanced visibility into production metrics and Key Performance Indicators (KPIs) allows for more accurate tracking of performance and identification of areas for improvement.
Cost Savings
Optimized Production Processes: Significant cost savings and increased productivity through real-time insights, resulting in reduced downtime and faster decision-making. Reduced Data and System Integration Costs: The seamless integration of OT and IT systems through i-flow and NATS reduces the time and resources required for data and system integration.
Scalability and Flexibility
Scalable Architecture: Combination of NATS and i-flow provides a scalable architecture that grows with the company’s needs. New systems and use-cases can easily be integrated without reconfiguration. Flexibility: The solution supports various communication protocols and data formats which ensures compatibility with different OT systems. This provides the flexibility needed to adapt to changing requirements.
Conclusion
Leveraging NATS for edge & enterprise-level messaging and i-flow for scalable integration significantly enhances manufacturing operations. This integrated solution offers real-time data processing, improved communication, and scalability, resulting in notable efficiency gains and cost savings for manufacturing companies.
About i-flow
i-flow is dedicated to empowering manufacturers with the world’s most intuitive software to seamlessly integrate factory systems at scale. Over 400 million data operations daily in production-critical environments not only demonstrate the scalability of the software, but also the deep trust our customers place in i-flow. Close cooperation with our customers and partners worldwide, including renowned Fortune 500 companies and industry leaders such as Bosch, Sto and Lenze, is at the heart of our business. Industry 4.0 enthusiasts love i-flow due to:
- Simplicity by Design: i-flow prioritizes ease-of-use, enabling customers to connect OT and IT systems effortlessly, avoiding technical hurdles.
- Unlimited Connectivity: The software boasts over 200 connectors for common OT and IT systems, significantly reducing the effort and time required to integrate and connect different systems and processes.
- Real-time Monitoring: i-flow offers crucial real-time insights and metrics, allowing users to optimize and maintain their digital ecosystems with ease.
Back to Blog